When designing sheet metal components, it is crucial to consider various factors that influence the quality and functionality of the final product. For example, k-factor, bending tolerances, material selection and press brake configuration can have a significant impact. If you want to delve deeper into this last aspect, find out more about the different types of bending machines that exist on the market.
Today we will talk about the K factor, because it is a fundamental element in bending and is closely linked to springback, a concept that you can learn more about in this article.
What is the k-factor?
The K factor represents the ratio of the neutral axis location to the material thickness during bending. It indicates how a material will behave under tension and compression forces during the bending process. The neutral axis is the imaginary line within the material that experiences neither tension nor compression. Accurately determining the neutral axis is essential for calculating the bend allowance, which is the additional length required to form a bend.
What is the neutral axis?
The neutral axis is the ideal area that does not vary during bending, and neither shortens nor lengthens. Do you want to know more about the neutral plane? We have written an article that goes into this topic in more detail.
Broadly speaking, we can say that in the vast majority of cases the neutral plane lies at about 1/3 of the thickness from the inside, so it is 0.33.
E.g.: a thickness of 30/10 will have t = 1 mm, so 1/3 = 0.33 = k
Nevertheless, there are cases in which the neutral radius tends to shift towards the centre, i.e. when the ratio
r/T > 1
Where r is the inside bend radius and T is the thickness.
Simplified Explanation of k-factor
Think of the K factor as a fraction: the distance from the inside of the bend to the neutral axis divided by the material thickness. For most materials, the K factor is approximately 0.33, meaning the neutral axis is located about one-third of the material thickness from the inside of the bend. However, factors like material type, bend radius, and bending process can influence the actual K factor.
Factors Affecting the K Factor
Several factors influence the K factor, including:
- Material: Different materials have varying K factors due to their unique mechanical properties.
- Bend radius: A smaller bend radius generally results in a higher K factor.
- Bending process: Air bending, bottom bending, and coining produce different bend results and thus affect the K factor.
Calculating the K Factor
The following formula is used to calculate the sheet metal layout:
k = log(r/s)x0.5+0.65
In any case, this table provides a set of values that can be used once you have the right inside bend radius.
Sheet metal k-factor table
0,65>r/t<=1 |
k=0.3 |
1 |
k=0.35 |
1.5 |
k=0.4 |
2.4 |
k=0.45 |
3.8 |
k=0.5 |
K Factor Calculation Simplified: VICLA's Online Calculator.
Streamline your bending operations with our free K factor calculator. Input material properties and bend geometry to obtain accurate results: vicla.eu/en/calculators/calculate-k-factor
Reverse Engineering The K-factor
Calculating the k-factor for your sheet metal bending operations can seem daunting at first. Essentially, it's a way to account for the material's behavior during bending, ensuring your CAD models accurately predict the final dimensions of your parts.
Here's a practical method to determine the k-factor:
-
Prepare a Test Strip: Start by cutting a strip of the material you'll be working with. Measure its length and thickness precisely. The width isn't critical, but a standard width like 100mm (4 inches) usually suffices.
-
Perform a Test Bend: Bend the strip at a 90-degree angle. Carefully measure the lengths of the two sides of the bend (let's call them Length X and Length Y).
-
Calculate the K-Factor: While the exact bend radius can be tricky to measure, it's not as critical as you might think. The k-factor you calculate will inherently account for minor discrepancies in the actual bend radius.
The key is to find a k-factor that, when used in your CAD software with your typical bend radius, accurately predicts the real-world bend dimensions you just measured. This means that even if your real-world tooling radius differs slightly from the radius you input into your CAD software, the calculated k-factor will compensate for this difference.
The formula for calculating the k-factor is:
K-Factor = (-BendRadius + (BendAllowance / (π * BendAngle / 180))) / thickness
where:
-
- BendAllowance = (2 * OutSideSetBback) – BendDeduction
- OutSideSetBback = (Tan(BendAngle / 2)) * (thickness + BendRadius)
- BendDeduction = Length X + Length Y - Total Flat Length
Validate and Adjust
If your calculated k-factor falls outside the acceptable range for your CAD software (usually between 0 and 1), double-check your measurements and calculations. This method provides the most accurate k-factor for your specific material and bending setup.
Developing a Sheet Metal Blank: The Role of the K Factor
There are several methods used in sheet metal fabrication workshops to determine the correct blank size for a bent part. While modern software tools have become increasingly popular, many shops still rely on empirical methods and experience.
Traditional Methods:
- Empirical Tables: These tables are created by conducting physical tests to determine the necessary compensation values for different materials and bend radii. Compensation values are added to the inside bend dimensions to account for material stretching during the bending process.
- DIN Tables: Similar to empirical tables, DIN tables provide values that are subtracted from the outside dimensions of the bent part.
- Geometric Calculations: Using the calculated K factor and the bend radius, engineers can determine the bend allowance through geometric formulas.
Advanced Methods:
- Software-Based Calculations: Modern CAD software can automatically calculate bend allowances based on the material properties, bend radius, and K factor. Designers can adjust the K factor to fine-tune the results.
- Percentage Method: A widely used method where the inside bend radius is simplified based on the die and material, and then the appropriate K factor from a table is applied.
Applications of the K Factor in Sheet Metal Fabrication
The K factor is a critical parameter in various aspects of sheet metal fabrication, including:
- CAD Design: CAD software uses the K factor to generate accurate flat patterns for bent parts.
- Part Production: The K factor ensures that fabricated parts fit together correctly without requiring post-production modifications.
- Prototyping: The K factor helps to verify the feasibility and accuracy of bends during the prototyping phase.
Understanding the K Factor
By grasping the concept of the K factor and its calculation, you can accurately determine the required blank size for your sheet metal bending operations. This ensures precise part production and reduces the need for costly rework.
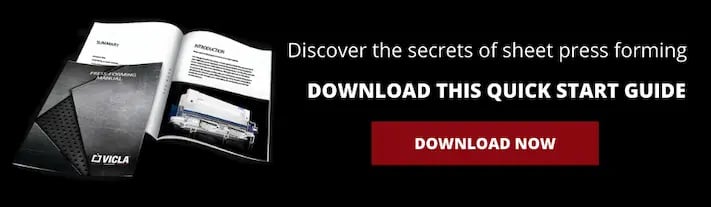