During the bending process, the machine is subjected to a tension that causes a deformation of the structure and, consequently, also of the sheet metal; to compensate for this kind of stress, the crowning system comes into play.
When we bend the sheet metal with a press brake, the upper crossbar always tends to curve upwards.
The crowning system lifts the die to maintain a constant distance between punch and die. Without it, the result of the bending angle would be irregular.
To put it in a nutshell, in a press brake with incorrect crowning or without crowning, the bending result will have a more open or closed bending angle.
For this reason, it is of fundamental importance to choose the correct crowning system for your press brake.
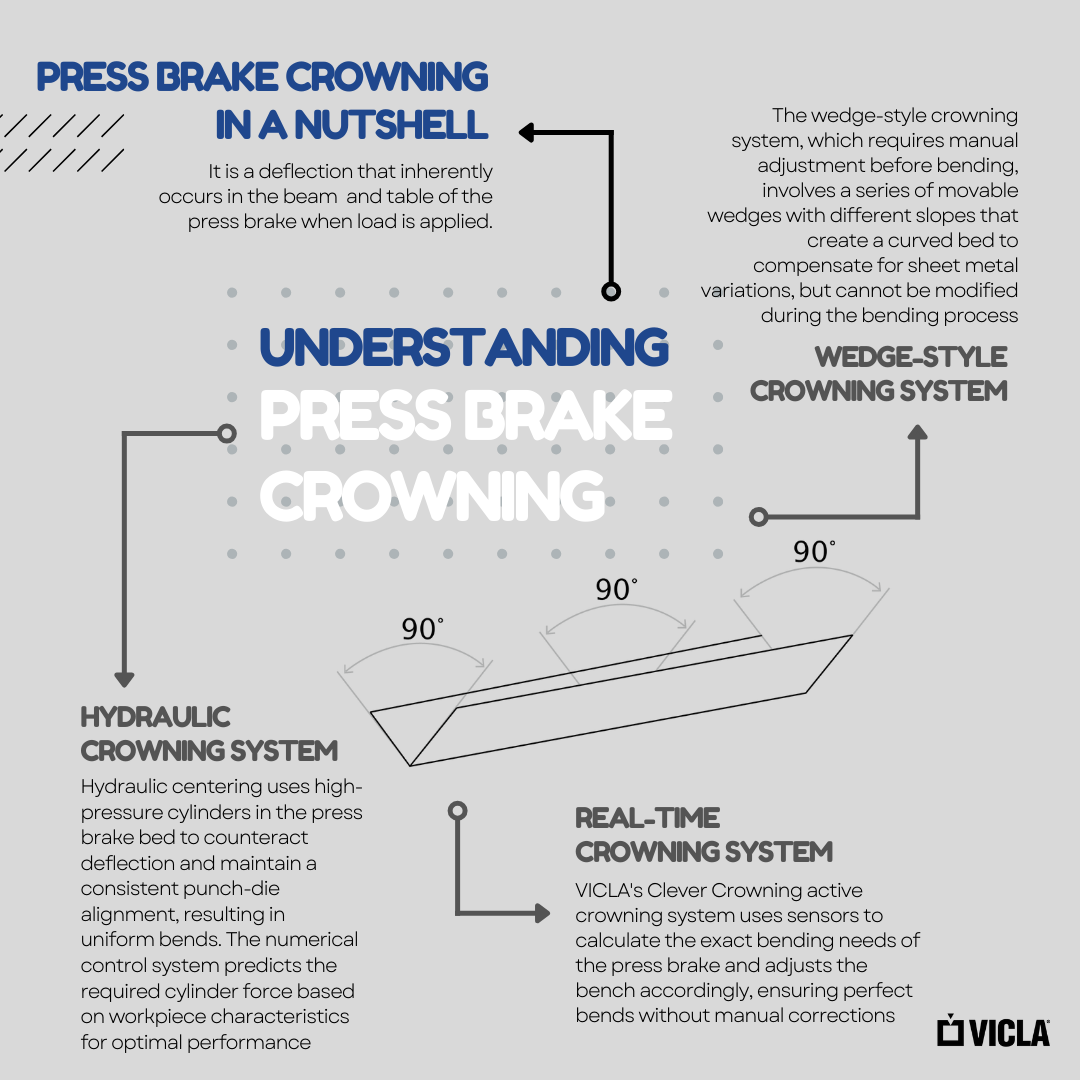
What are the main crowning systems?
There are several crowning systems, some of which are exclusive patents of very few manufacturers such as VICLA.
Today you will discover the three main systems and which, among them, really helps you to achieve perfect folds without having to waste material and money on tests and verifications of the part.
If you want to read immediately what it is, you can go directly to the paragraph where it talks about active hydraulic crowning.
Wedge-style crowning system
The wedge-style crowning system is an adjustment that takes place beforehand and can be modified on the basis of the characteristics of the sheet metal.
It consists of two rows of wedges across the length of the bed; one row is fixed and the other is movable; moreover, it involves a series of profiles with different inclinations, characterized by a stronger marking in the center and less on the sides.
The wedge in the middle of the bed has a higher slope than the wedges under the pistons, and the angle of the slope decreases toward the ram from the middle of the bed.
On one of the sides of the machine there is a gear motor: when activated, the movable wedge creates a curve with the high point at the center of the bed and the low points at either end of the bed below the pistons to create a spline curve in the table.
The wedge bench always requires an intervention by the operator; In fact, the profiles, when viewed from the side, show an oblique contact plane that allows the expert bender to adjust the rib and make it localized.
This system, while very useful, has one major drawback.
With the wedge table, changes to the linearity of the bench cannot take place during bending, but must necessarily be made beforehand. In fact, this crowning system is also called pre-crowning, precisely because the adjustment takes place before starting to bend the sheet metal.
Sheet metal bending and crowning: how much do you need to compensate?
Compensation is one of the crimper's big pet peeves. While it is true that there are theoretical tables and formulas to calculate compensation, it is equally true that sheet metal is an unpredictable material.
It happens very frequently that the theory clashes with the variable behavior of sheet metal. What can be done in these cases?
Surely the first step to take is to know all the factors that determine the behavior of the sheet metal. It will help you understand how to compensate for them and not waste time and material on tests and verifications. Sometimes, however, even knowing the material is not enough and the company could run into many problems deriving from non-uniform parts: material cost, late deliveries, high waste.
Getting the result right the first time becomes essential for companies that want to remain competitive in the market.
Crowning systems: hydraulic crowning
Hydraulic crowning is a system historically used by many manufacturers.
Inside the bench, in the table that bears the stress and supports the dies, high-pressure and low-flow cylinders are inserted. Like real hydraulic jacks, they push the center of the bench upwards, thus compensating for the deformation of the stomp.
The effect you get is the perfect parallelism between the punch line and the die line.
With hydraulic crowning, you get a workpiece with a constant bend between the center and the sides.
Even in this case, however, it may happen that, due to the variability factors of the sheet metal, the system returns a value that is not optimal. In fact, the numerical control calculates the compensation on the basis of the description of the piece to be produced and on the calculation calibrated to the structure of the sheet metal machine.
Linear bends of sheet metal at the first attempt: active hydraulic crowning
The only way to successfully manage crowning is to use technology that measures the actual deformation and corrects it in real-time.
VICLA, for this reason, can guarantee active crowning, which, in fact, represents the evolution of the system and the ultimate in terms of repeatability and precision. With VICLA's Clever Crowning active crowning system, you can be sure that no matter how different the material is, you will always achieve a perfectly linear crease.
How does the active crowning system work?
VICLA's Clever Crowning active crowning is a sophisticated and extremely intelligent system that provides for a modification of the linearity of the bench, calculated exactly on the basis of the real need.
The press brake, in fact, thanks to special sensors inserted at the strategic bending points, is able to understand exactly how many hundredths of a millimeter the extent of the crossbar bending is.
It is no longer a parametric calculation, but a real value that establishes the exact pressure that the cylinders must use to compensate for the bench and achieve the perfect bends along the entire length of the profile. This solution does not require corrections because it is positioned completely automatically, always guaranteeing excellent results.
In short, it is a real revolution in the bending process that improves work in the workshop in many ways:
-
you get excellent results even with inexperienced staff, as the system calculates everything automatically;
-
reduce material waste, as the system applies the exact compensation in real time;
-
reduce production times because you no longer need pre-crowning and part checks.
All the systems currently offered on the market, hydraulic or mechanical wedge, require corrective intervention by the operator. They are therefore semi-automatic systems, in which the positioning is theoretically determined by the NC but is subsequently corrected by the operator.
With VICLA's Clever Crowning active crowning system, on the other hand, the NC measures the changes to be made in real time without you having to intervene with subsequent adjustments. This option is available on the hybrid press brake. SUPERIOR and allows you to achieve exceptional performance.
Now that you know how to achieve perfect folds without wasting time and material, discover the other benefits of VICLA press brakes.
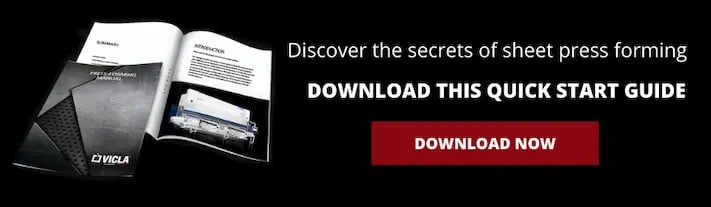